Tata International, Dewas
Gani Robotics takes a platform approach to build our products and turnkey solutions. Leverage our solutions to optimization the business throughout your value chain.
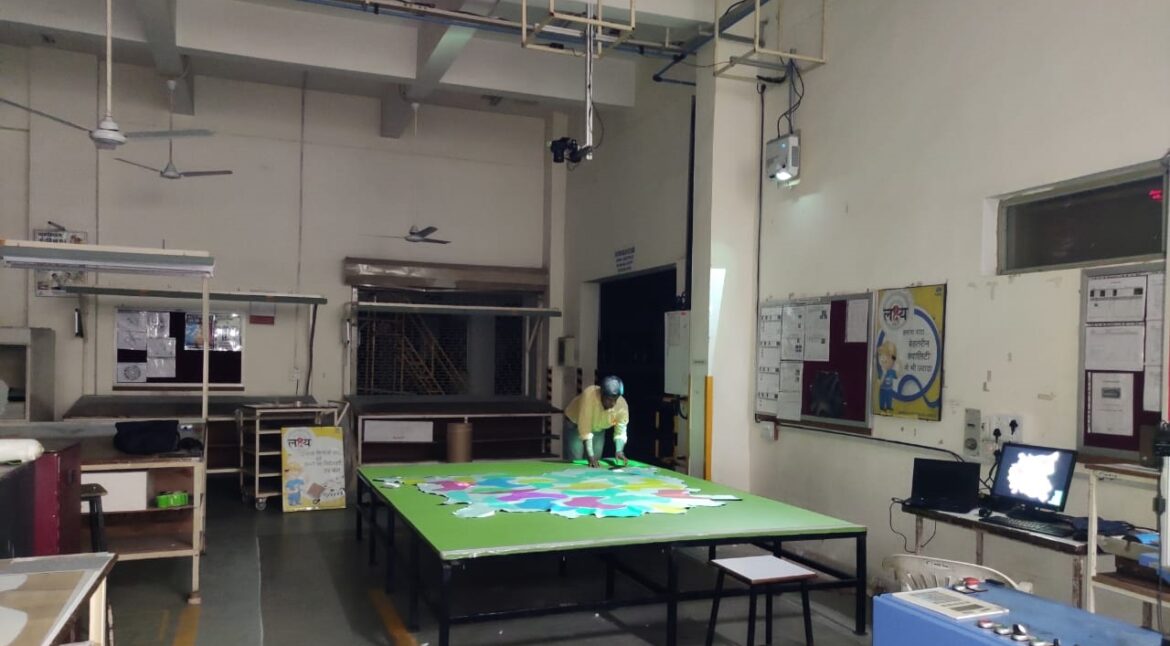
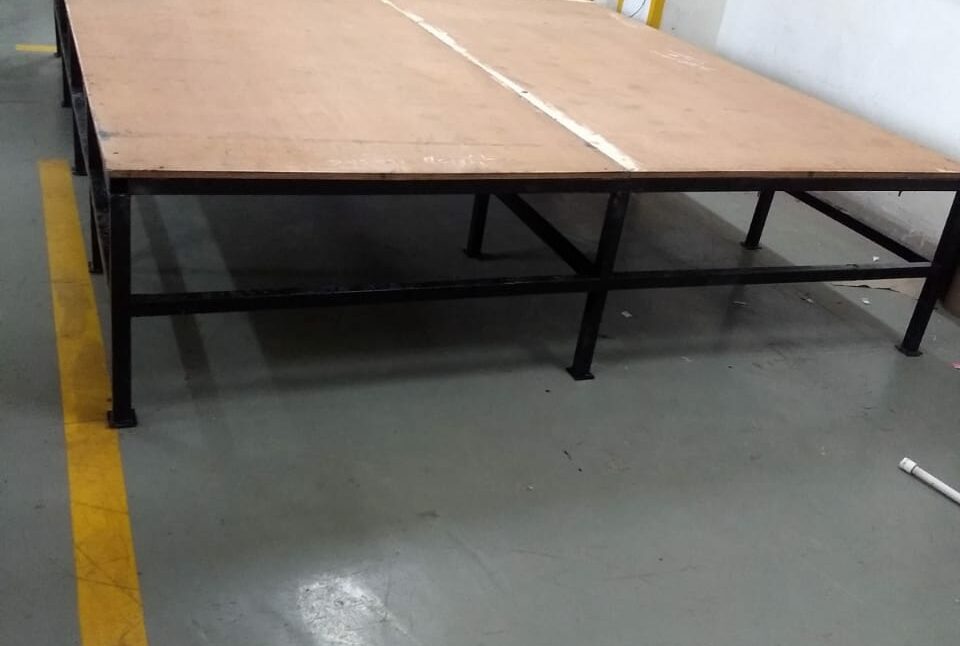
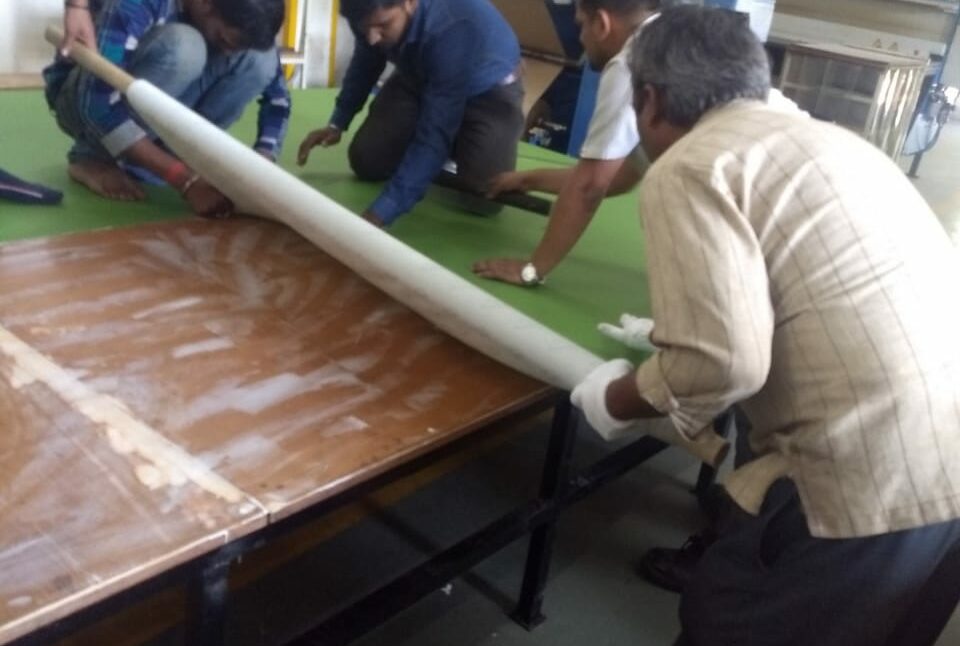
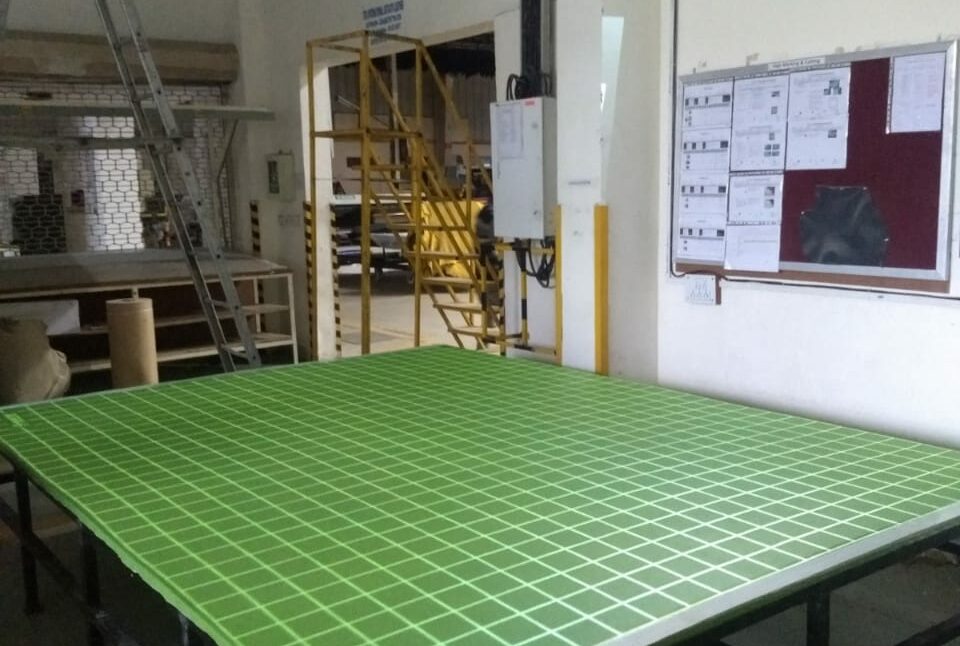
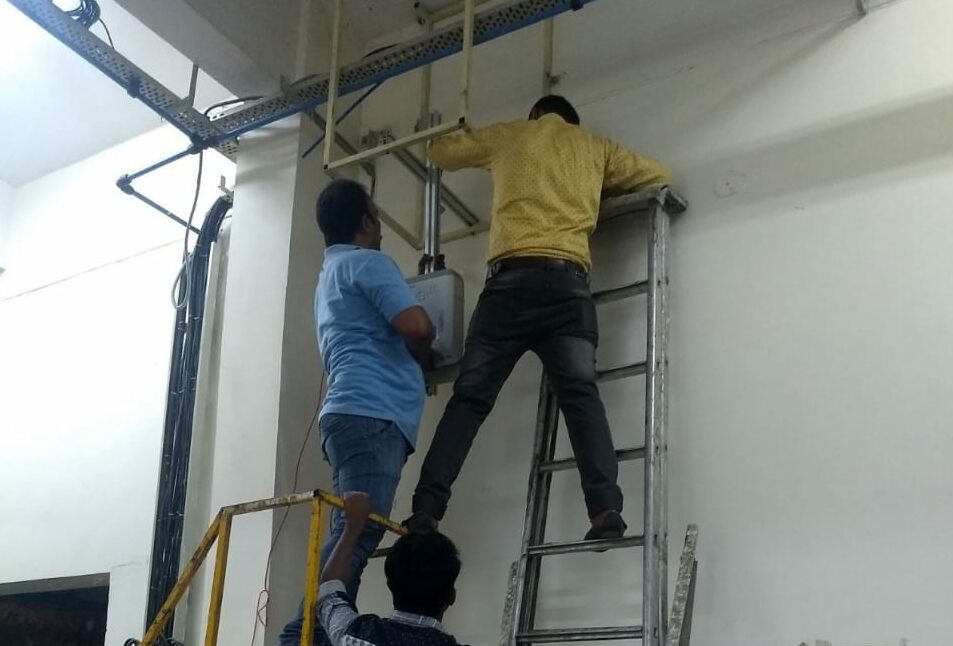
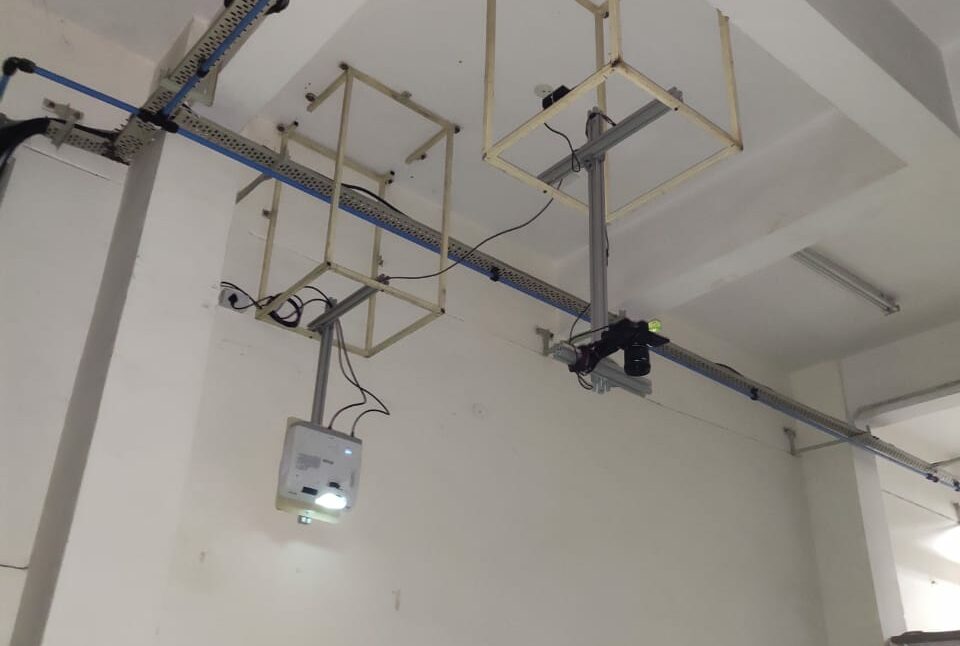
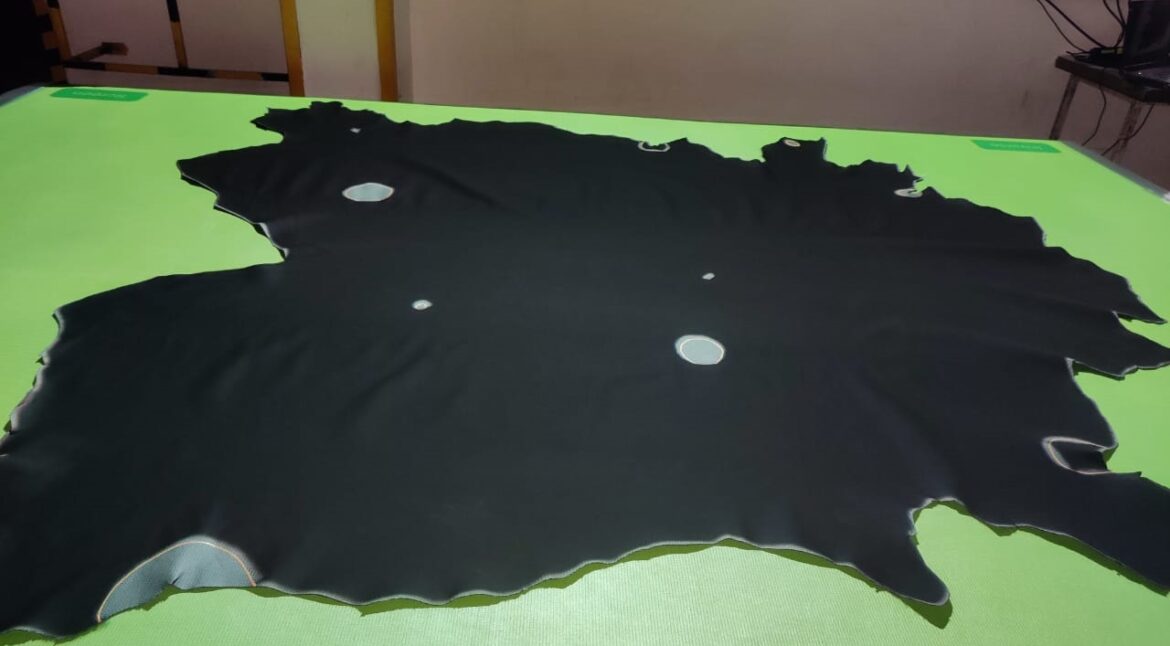

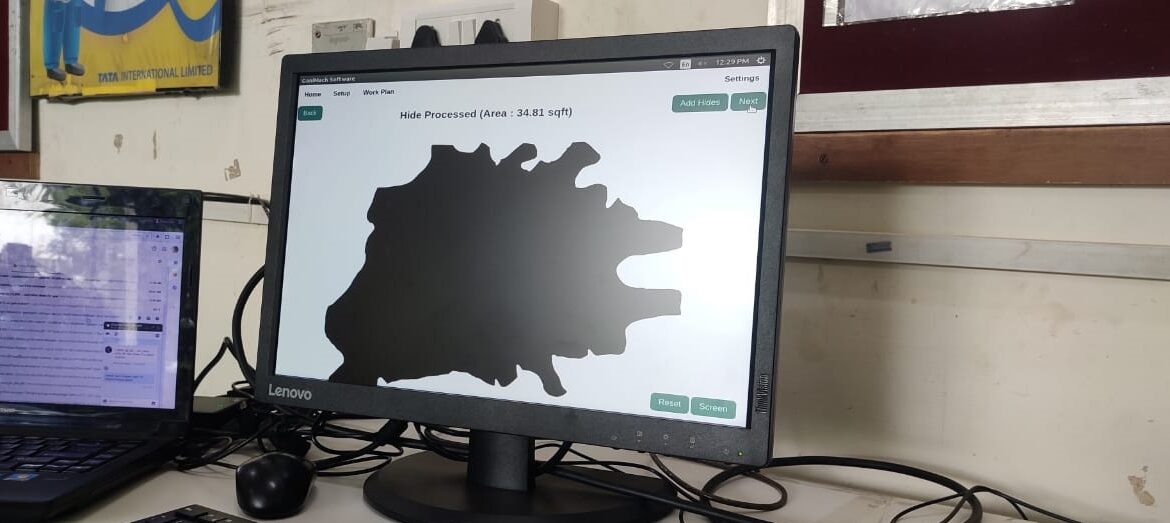
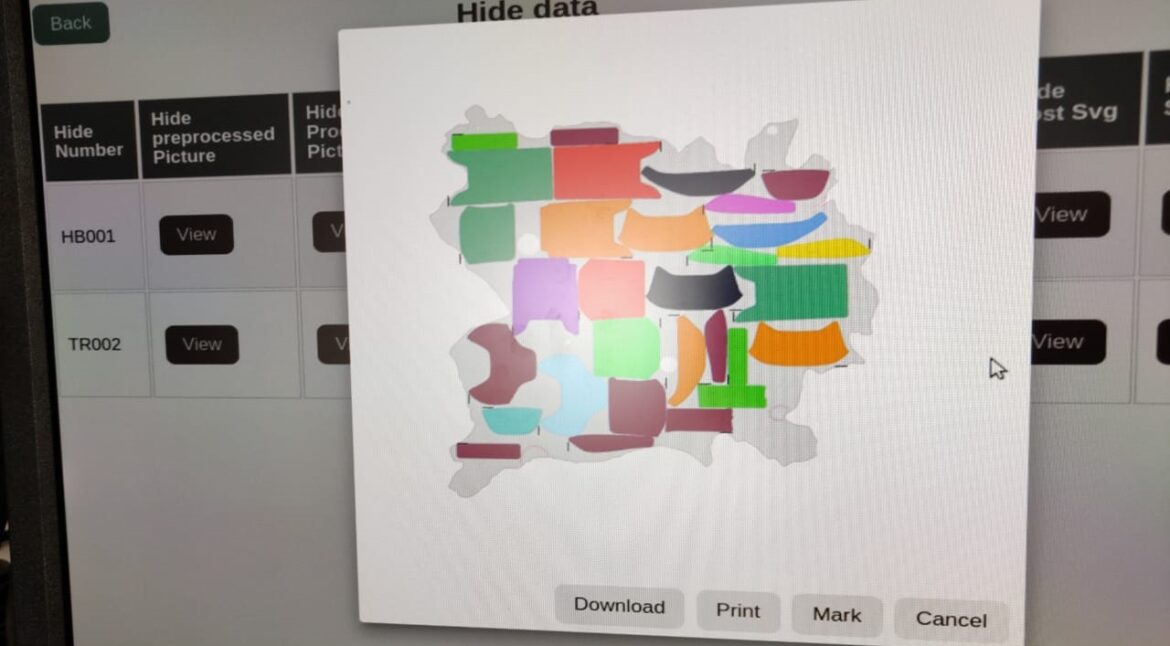
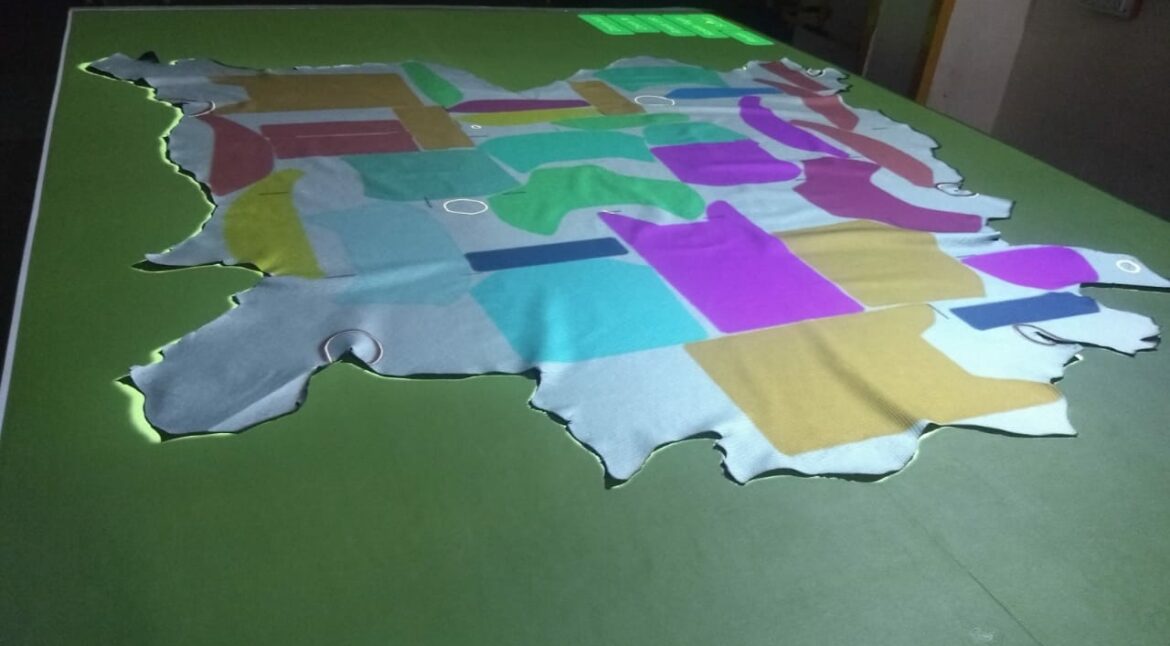
Brochure
Download our brochure to explore our products, solutions & services we provide
LET’S OPTIMIZE YOUR PRODUCTION
Please feel free to contact us. We will get back to you with 1-2 business days. Or just call us now.
About the Problem
Cutting floor in leather industry is more of human intensive process with no proper indicators to get effective material utilization. Since leather is a natural product one can expect irregular profile, defects and presence of different quality areas.
Currently hides are issued to cutting floor where nester does the placement of shapes or templates manually using trial & error and by his level of experience. He then marks the leather hide with templates in place and given to the cutter. Cutter then cuts the shapes on the hide using clicking die. In some production floor step 2 and step 3 carried out by the cutter itself.
All the above activities are are carried out manually and sub-optimal. Due to this factory can’t track wastage, efficient material usages and also proper forecasting is not possible. Our GaniCRP provides the solution to semi-automate/automate the above said process by using vision based solution and nesting software.
Client’s Challenge
Tata International produce finished leather hides of up to 60 Sq. ft. area which are cut into specific shapes and size as per the customer requirements mainly for automotive industry. There are about 20 to 40 different shapes that are requested by the customers. One such set of shapes is called a Kit. These shapes are cut from the leather hides. Area of leather hides are chosen to accommodate to cut all shapes from one kit.
Another challenge is entire kit need to be cut from maximum of one or two hides in order to keep cosmetic texture differences minimal. Operator will try to cut all shapes from one kit in one hide. If any spaces left in first hide shapes from second kit are placed to cut. Similarly if any shapes can’t placed in first hide then it is placed on priority in second hide. This process is goes similar way for all subsequent kits till everything is processed.
Shapes are cut manually by the operator using trial and error method and by his experience. First, the operator places the templates on the given leather hide one by one. He then cuts the hide with knife one by one. This process is not optimal since the shapes are cut one by one and skill of operator differs based on environment. This result in low utilization of raw material hide and inconsistent outputs.
Our Approach And Solution
We proposed our GaniNest product customised to suit sequencing requirement of the customer. Along with custom nesting solution we also integrated our other products in to one package. One package is called GaniCRP – Cut resource planning software offers a complete solution for import of models, automatic nesting of patterns, projection, manual print guidance for cutting, analytics, reports and supervision of a cutting process.
GaniPattern
Photo-digitization of Patterns
Fast & Easy way to input patterns to the database
GaniScan
Photo-digitization of Leather
Digitization of leather hides using DSLR Camera
GaniNest
Automatic Nesting Station
Fully Automatic Nesting with Industry best efficiency.
GaniProjection
Hide Projection Station
1:1 hide projection for digital die cutting using roller press
Print Module
Nested Hide Print Module
Nested hides are printed in A2 sheets for guidance to operators
GaniCRP
Cut Resource Planning
Complete statistics and analysis of production data