GaniNest – Leather Nesting Machine
GANINEST – Leather Auto Nesting Software gives you significant improvement in your factory revenues by optimizing the whole cutting room in terms of increasing leather savings, low labor cost, increased productivity and more
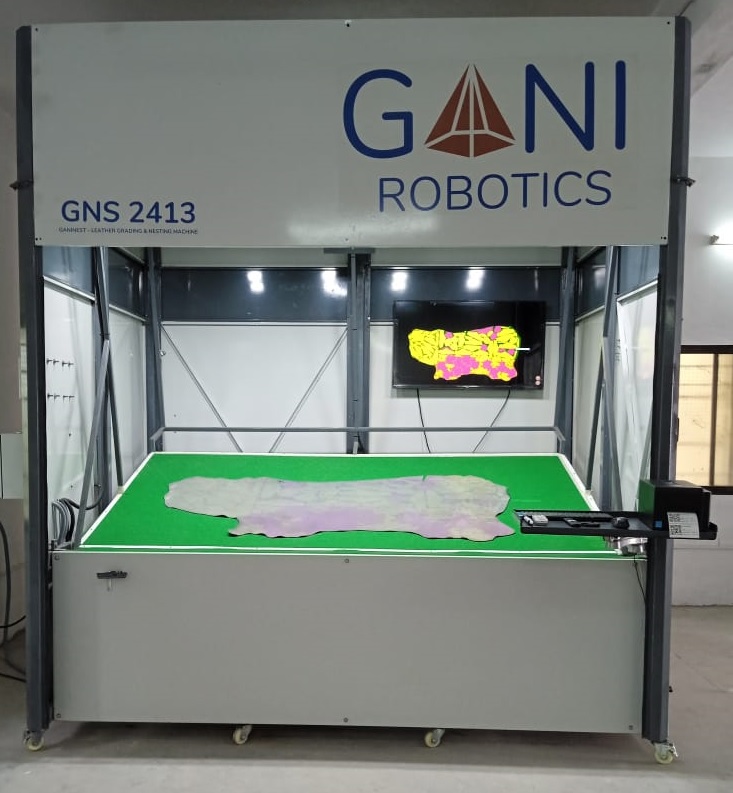
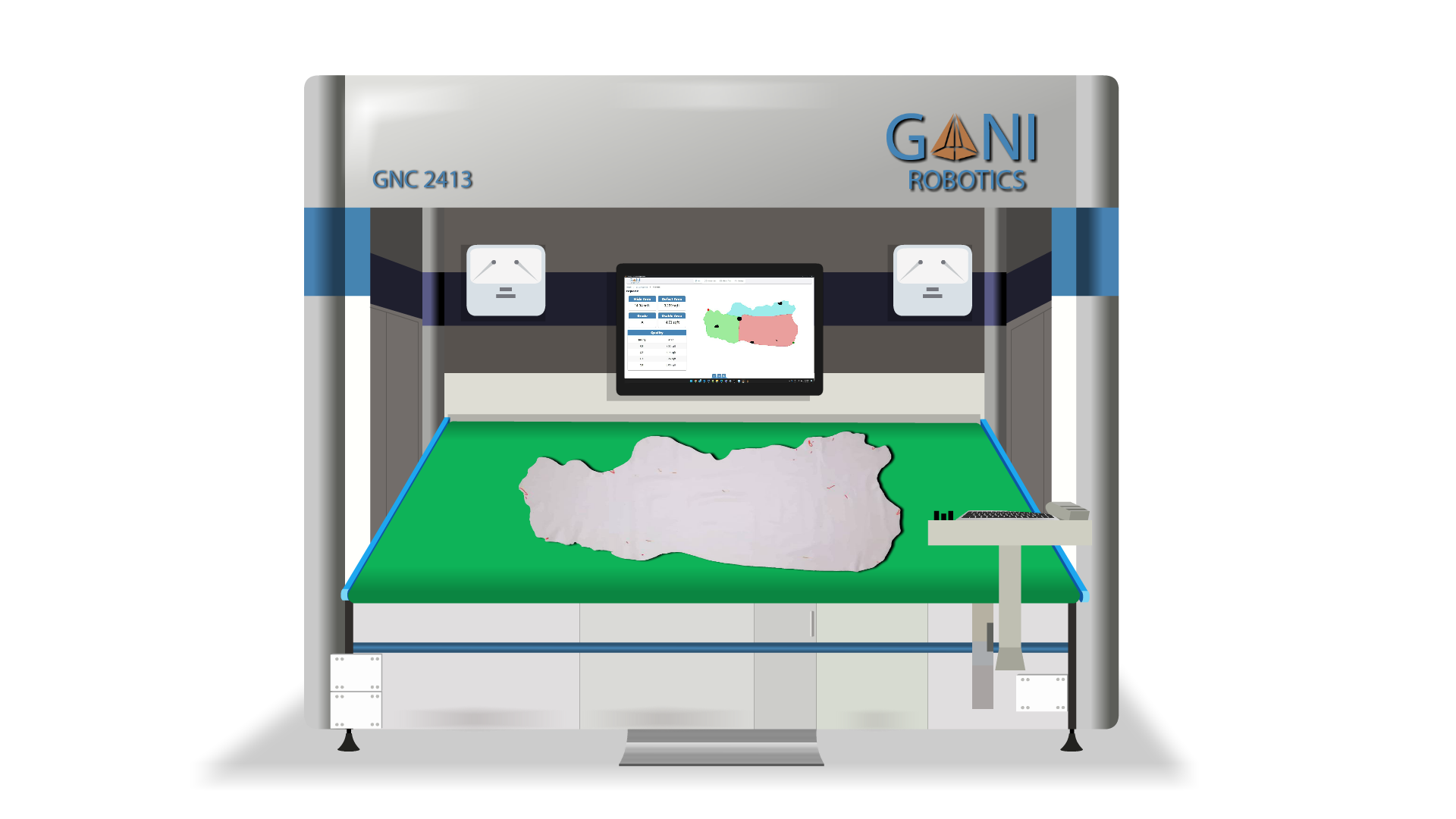
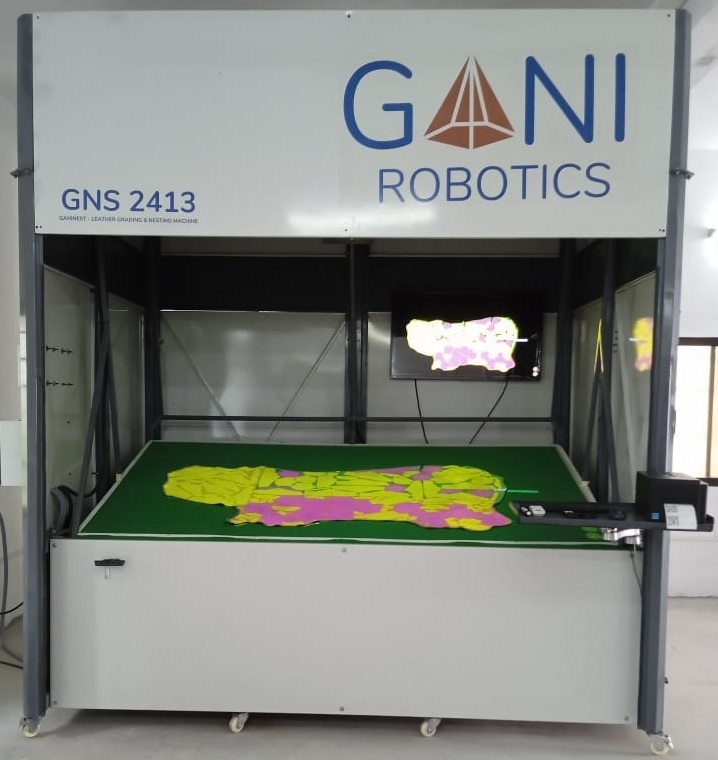
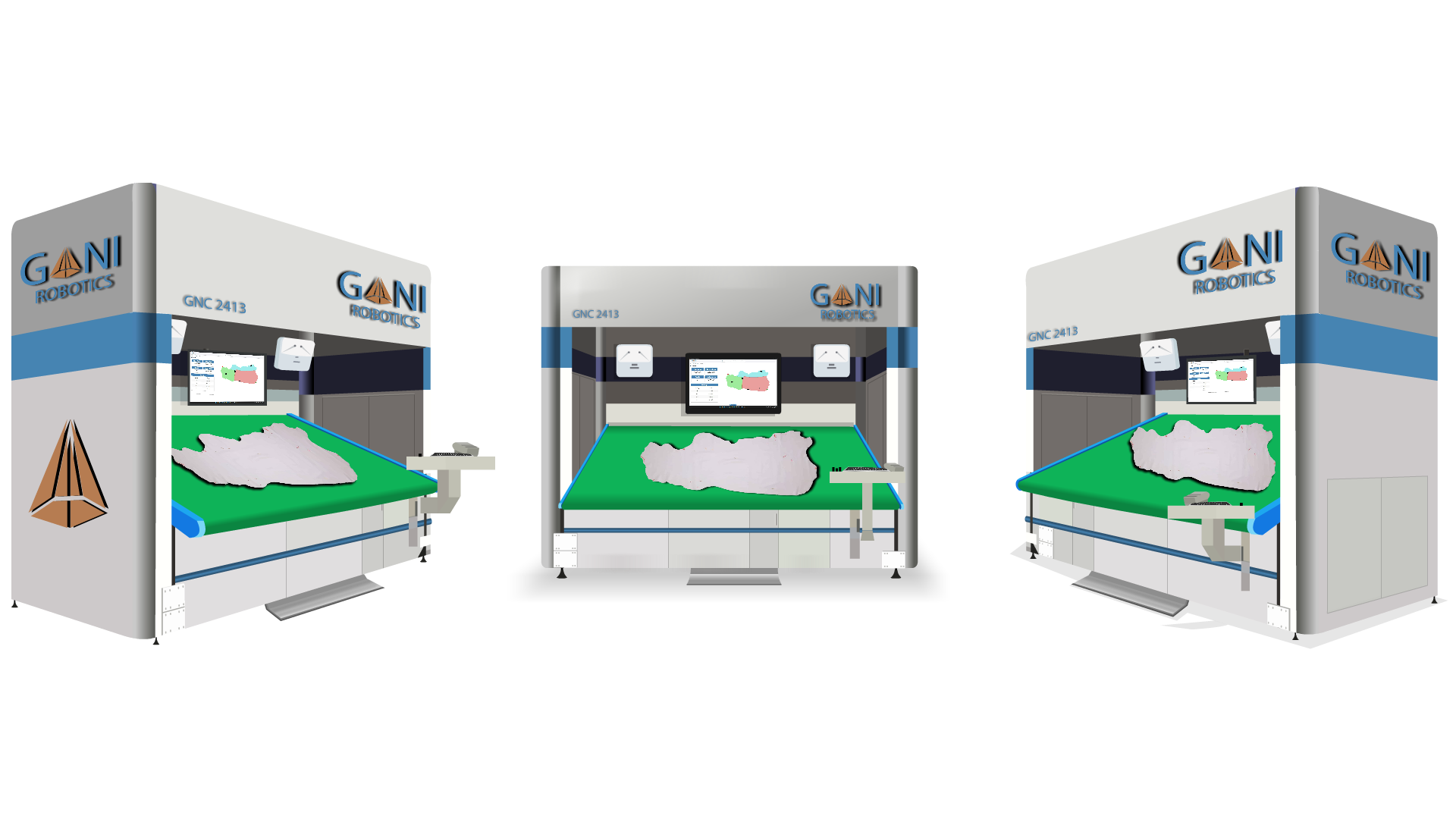
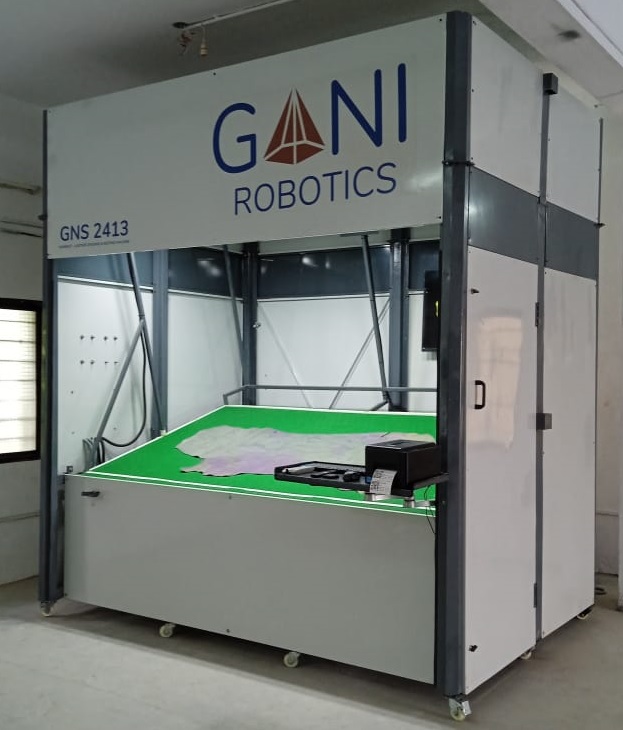
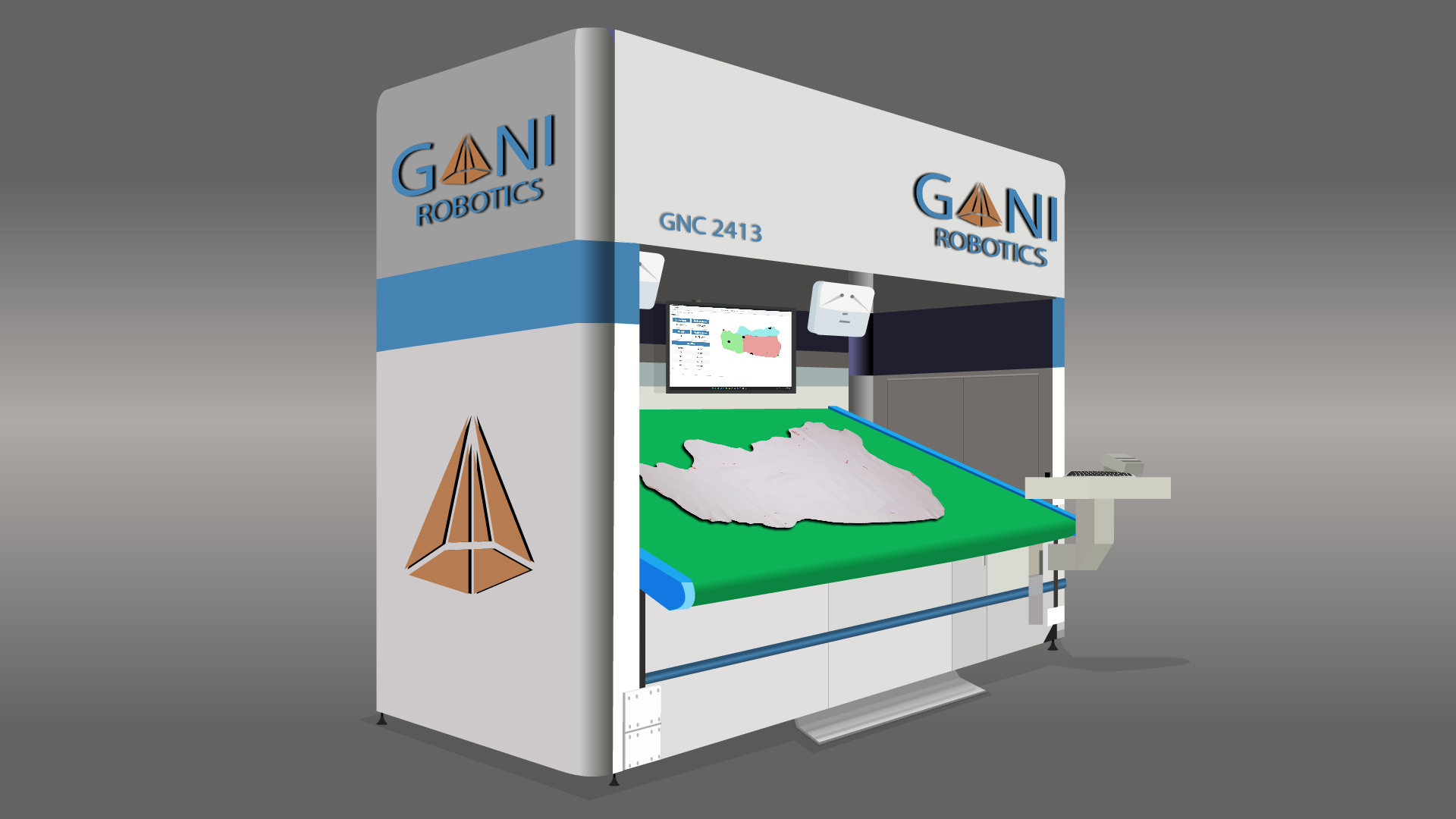
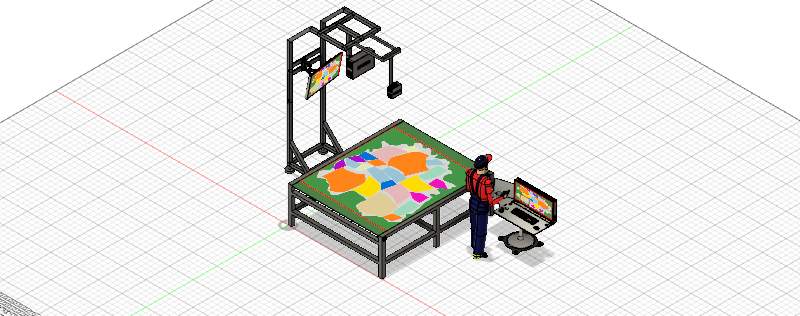
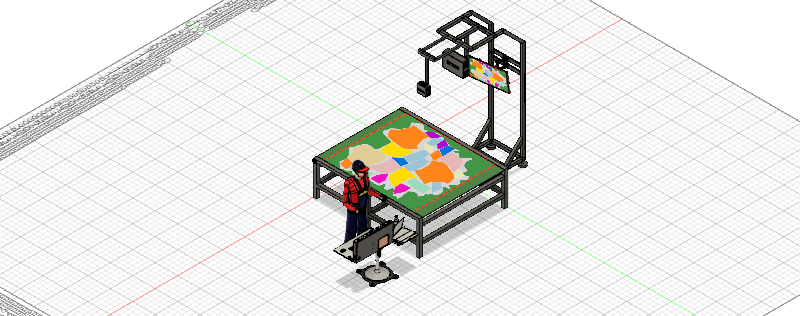
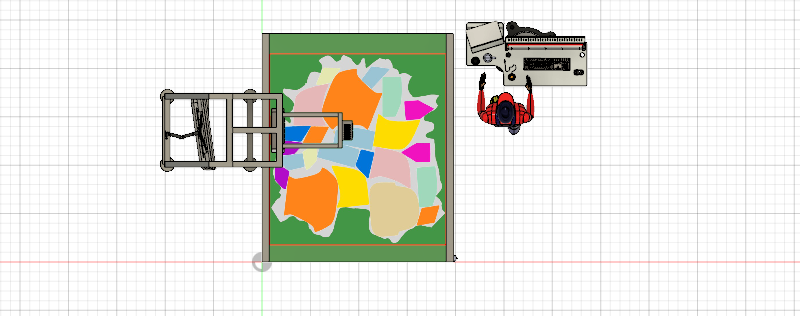
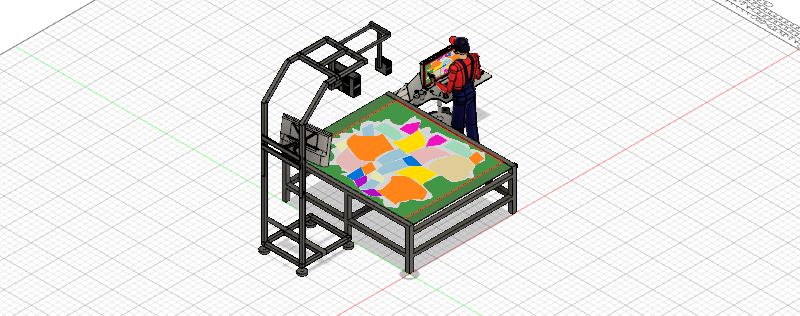
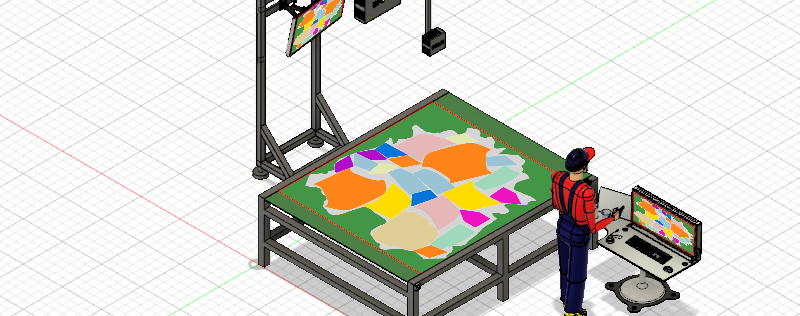
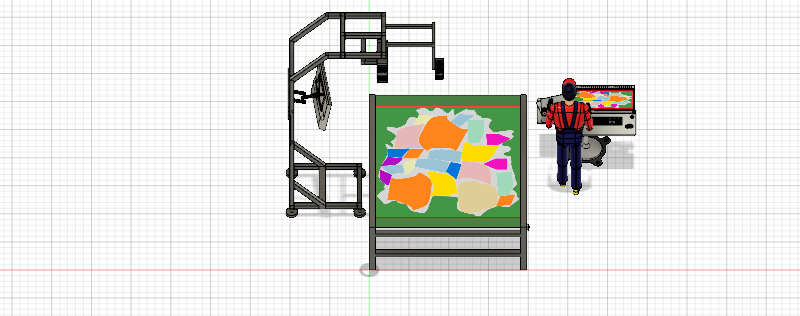
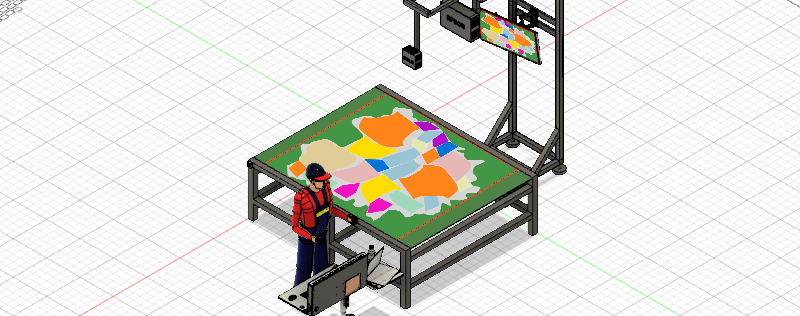
Brochure
Download our brochure to explore our products, solutions & services we provide
LET’S OPTIMIZE YOUR PRODUCTION
Please feel free to contact us. We will get back to you with 1-2 business days. Or just call us now.
GaniNest – Leather Nesting Machine
Cutting floor in leather industry is more of human intensive process with no proper indicators to get effective material utilization. Since leather is a natural product one can expect irregular profile, defects and presence of different quality areas.
How GaniNest helps?
GANINEST – Leather Auto Nesting Software is one integrated system which gives you significant improvement in your factory revenues by optimizing the whole cutting room in terms of increasing leather savings, low labor cost, increased productivity and in turn high manufacturing throughput
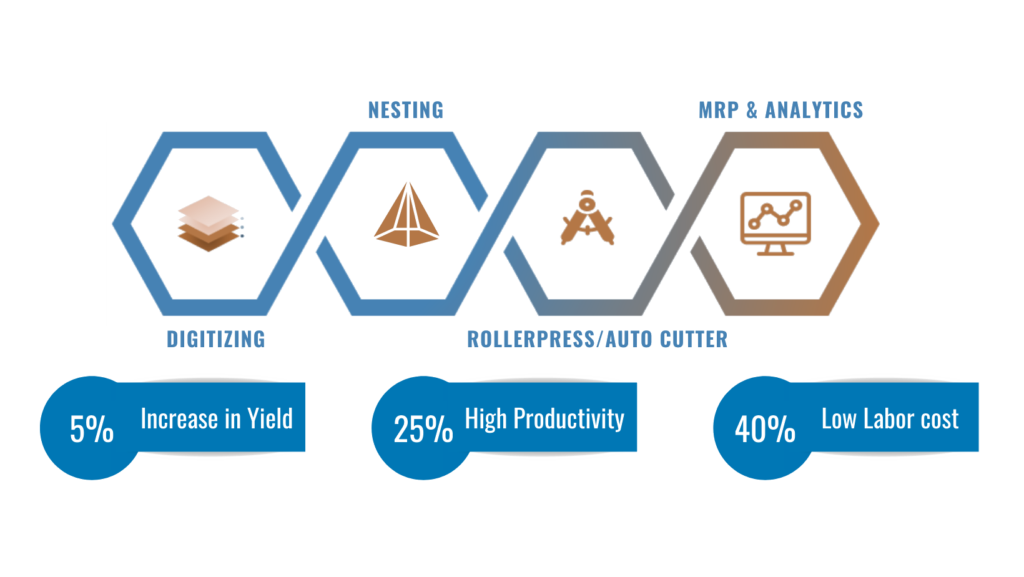
Industries suitable for this solution
GaniNest Integrations
Die Clicking Press
GaniNest Model Variations
Static Bed Model
Machine Cabin Model
Features
Grader can easily mark the defect interactively using digital pen projector combination OR touch screen monitor or mouse/monitor combination. Options like type of defect classification zoom in, pan the image makes it easy
Auto defect Identification using colored chalk markers. Manual leather grading process can be used to identify quality regions.
Hide regions can be classified and assigned with different quality/template regions like neck, shoulder, butt, belly regions
Patterns can be easily imported to our system or it can be digitized using our optional GANIPATTERN modules.
Operator can mark and classify the defects as D1 and D2. D1 means high grade defects where no parts can be nested and D2 means low grade defects where parts with low qualities can be nested
Patterns can be assigned to quality regions where only it can nest, rotation, gap between patterns etc
High efficient multi core nesting algorithm finds best optimized placement avoiding defect regions.
Interactive workspace is provided where you can do manual nesting as well. It can help you to place some priority parts prenested then give auto nesting. It also helps to do post auto nesting adjustments.
Operator can snap the hide, mark the defects, assign quality regions and add to the queue. All this while nesting for previous hide is running in background process.
Multiple projects can be created and assigned with order plan. Hides can be digitized and add to the projects and can able to give batch nesting at one go.
Easy and Customisable workflow to suit your existing cutting room process.
Planning & optimizing the shop floor resources like raw materials, machines and operators.